Can “Phase One Step†polycrystalline lead in the next few years?
2023-12-12 08:08:17
Abstract In the photovoltaic industry, monocrystalline and polycrystalline components have always maintained a competitive pattern. Who can better meet the needs of the future market? In the past, relatively small monocrystalline components in the market share Some improvement, this change is a long-term counterattack of single crystal...
In the photovoltaic industry, monocrystalline and polycrystalline components have always maintained a competitive pattern. Who can better meet the needs of the market in the future? In the past, relatively small monocrystalline components have market share. Elevated, is this change the beginning of a long-term counterattack of single crystals, or is it a short-lived difference between the two? Many industry insiders said that PV modules are essentially an emerging power generation equipment, and the price/performance ratio is the key to the market. Because there is no personalized experience in power products, some are only based on the country. Voltage and frequency. Only by twisting the "cost-effective" beef nose can we see the fog of the single-crystal battle of photovoltaic modules.
2015, single polycrystalline force re-segmentation
In the first quarter of 2017, monocrystalline silicon wafers in the photovoltaic market continued the trend of hot demand in 2016. Industry research institutes predict that the shortage of monocrystalline silicon wafers will continue until the new capacity of the two major monocrystalline wafer plants in Longji and Central are released in the second quarter. With the promotion of the front-runner project and the tightening demand for monocrystalline silicon wafers in the market, the voices of single crystal products in the industry are getting hotter and hotter, and there is a tendency to cover up the polycrystalline products that originally occupied the main market.
Looking back on the past 10 years of the photovoltaic industry, this round of single crystal hot market started in 2015. According to data released by EnergyTrend, the proportion of monocrystalline silicon wafers in the world rose to 18% in 2015, and the proportion of polycrystalline silicon wafers decreased to 76%. In the past 2016, the market share of single crystal has further climbed to more than 20%.
For the rapid development of single crystal, Wang Shijiang, deputy secretary-general of China Photovoltaic Industry Association, said: "The key to the rise of single crystal products since 2015 is that the breakthrough in technology will drive down the cost, which is manifested in two aspects, the first monocrystalline silicon wafer. The transformation from the mortar line to the diamond wire has been completed, which has improved the cutting efficiency by more than 50%. The second is the continuous crystal pulling process, which improves the productivity of the single crystal silicon rod, and the output is improved and the cost is reduced."
According to PV-Tech, the diamond wire has the characteristics of fast cutting speed, small wire diameter, no need for mortar in the cutting process, and low content of surface metal impurities. In the middle of 2014, domestic monocrystalline silicon wafer leading enterprises represented by Longji and Central successively realized the introduction of diamond cutting, and achieved capacity release in 2015. In the 2014 announcement, Longji announced that it has reduced the thickness of the diamond wire slice from 190 m to 110 m. At that time, because downstream battery manufacturers were reluctant to accept thin silicon wafers, the introduction of diamond wire slices did not increase in equipment. Under, significantly increase production capacity. In 2015, Longji announced that all conversions were successful. On the basis of further improvement of the process, other companies have also invested and the proportion has continued to rise, and the situation in 2016 has exploded.
Black silicon cracked polycrystalline missed the pain of "golden wire cutting"
“'Jinang Line Cutting' is a major breakthrough in the reduction of single crystals. However, when this new technology was introduced into the production process of polycrystalline silicon wafers, it was once unacceptable,†said Lu Jinbiao, vice president of Poly GCL. The difference between the single crystal silicon ingot and the polycrystalline silicon ingot in the lattice structure and the internal dopant causes the silicon wafer to be cut into a polycrystalline silicon wafer, and the surface is too smooth, which poses a challenge to the subsequent battery process."
In order to solve the pain of polycrystalline "golden wire cutting", China's polysilicon wafer manufacturers have taken the lead in launching "black silicon technology" in 2016. Through black silicon texturing, not only can polycrystalline silicon wafers be introduced in mass production. Diamond wire cutting technology, and the photovoltaic power conversion rate of polycrystalline silicon cells increased by more than 0.3%.
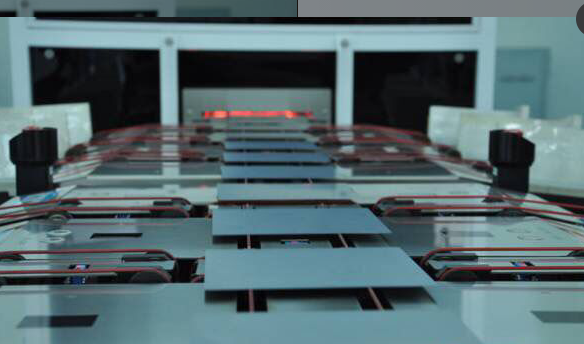
"Before the polysilicon wafer was not used for 'gold steel wire cutting + black silicon', the cost difference of the single polycrystalline silicon wafer was compressed to about 0.6 yuan per piece, which has broken the red line of the polycrystalline module with the power cost of the single crystal module at the power generation end. After GCL-Poly uses the "Gold Steel Wire Cut + Black Silicon" in the mass production of polycrystalline silicon wafers, the cost per wafer is reduced by about 0.5 yuan. In this case, the price of polycrystalline silicon wafers is about 1.1 lower than that of single crystal. Yuan. This allows polycrystalline components to return to 2015 as before, and achieves a significant price/performance advantage over single-crystal power generation costs," added Lu Jinbiao.
“After the breakthrough in the single crystal and the diamond wire cutting of single crystal, the new technology to promote the cost performance of single wafer is limited in the short term, and there will be no such big change in the previous two years.†CEO of GCL Integrated Technology Co., Ltd. Zheng Jiazhen, chief technology officer, believes that in the next few years, monocrystalline and polycrystalline will maintain a market pattern of 37%, and polycrystalline has room for further improvement, and its dominant market position will not change.
According to the latest market quotation in March 2017, due to the continued shortage of monocrystalline silicon wafers, the price difference of single polycrystalline silicon wafers has reached 0.17 US dollars / piece, which has exceeded the price/performance standard value difference of 0.1 US dollars. Subsequent single crystals want to increase the cost performance, and rely on new technology to reduce costs.
Although the single-chip sings in the market have been sung in recent days, it cannot be ignored that the production capacity of the top ten mainstream PV manufacturers and other second-tier manufacturers is still dominated by polycrystalline components. In order to enhance the competitiveness of polycrystalline components, domestic first-line PV manufacturers such as Jingke, Hanwha, Artes, and Trina have applied PERC technology to improve the conversion efficiency of polycrystals.
In May 2016, JinkoSolar announced that its high-efficiency polycrystalline battery using PERC and black silicon technology has entered the mass production stage, and will increase the photoelectric conversion efficiency of mass production cells to over 20.5% in the future. In June 2016, Hanwha New Energy stated that its standard PERC polycrystalline components have a conversion efficiency of 19.5% and a power of 301W. In August 2016, Artes said that its use of wet black silicon technology combined with diamond wire cutting can make the conversion efficiency of polycrystalline battery reach 19%, and the superimposed PERC technology can raise one point to 20%.
In this situation, EnergyTrend analyst Corrine Lin expects that black silicon products will be significantly heavy this year and next, so that polycrystalline silicon wafers can accept diamond-cut polycrystalline silicon wafers, and the overall polycrystalline module cost can be reduced by US$0.015 / W to counterbalance. The single crystal market accounts for a high growth.
"The leader" eats a long one
In addition to the priority progress of processes such as the Diamond Wire, another important driver of the rapid development of single crystal in the past two years is the maximum use of the "Leader Plan."
In June 2015, the National Energy Administration approved the 3GW National Advanced Technology Photovoltaic Demonstration Base in the Datong Coal Mining Subsidence Area in Shanxi, and the “Top Runner Program†officially started. In May 2016, the second batch of 5.5GW front-runner bases was announced, with a total market of 8.5GW, which attracted competition from industry players. Different from the past, technology has become one of the important indicators in addition to price competition.
According to the documents issued by the Energy Bureau, the "leaders" advanced technology products should reach the following indicators: the photoelectric conversion efficiency of polycrystalline silicon battery modules and monocrystalline silicon battery modules reached 16.5% and 17% respectively.
Lu Jinbiao recalled: "When the front runners planned to launch, in order to strive for more development space for single crystals, the efficiency requirements for single crystal modules were lower than those of polycrystalline modules when setting efficiency standards. Original single polycrystalline component conversion efficiency The gap is more than 1%, but in the release document, the difference between the two is only 0.5%. For the standard components of 60 cells, the total power difference between single crystals is only 5 watts."
"The policy tilt makes it impossible for single crystal manufacturers to achieve the leader's requirements without adding PERC. Polycrystalline is relatively difficult to meet the requirements. Therefore, in the 2016 leader plan, the proportion of single crystal market is gradually rising." The trophy emphasizes that the polycrystalline technology route has huge technological development potential and cost-effective advantages. In the next leader or super-run plan, the technical update and standard setting should set the total power difference of the single polycrystalline 60-cell standard components. It is 15 watts. This will enable both sides of the single polycrystal to form a true technological competition and promote the development of the industry.
In February 2017, the statement that the National Energy Administration will introduce the “Photovoltaic Super Leaders Program†has been discussed in the industry. It is said that the first batch of “Super Runner Bases†will be announced soon. According to market rumors, the "Photovoltaic Super Runners Program" is an upgraded version of the "Top Runner Program". It will support the production capacity of mass production, but the capacity has not been released, representing advanced technology, by building a "super leader base". The scale of photovoltaic products is applied, and the scale of each base is GW level.
The plan for the super runner has yet to be determined, and the industry has been in turmoil, and disputes over the development of rules and standards have begun. Industry analysts said that the development of the leader plan is based on the principle of normal distribution of component conversion efficiency. Whether it is single crystal, polycrystalline or thin film, it should be recognized that the high-efficiency products in the respective technical routes are in line with the leader plan. The requirements to lead the development of photovoltaic products to high efficiency.
Zinc Plated Threaded Rod,Threaded Screw Bar Studs Rods,Studs Rods Anchor Clamps Hangers,Right Hand Threads Threaded Rod
Handan Jiankun Hardware Products Co., Ltd / Handan best import and export trade co., Ltd , https://www.jkscrew.com