There are many kinds of plastic additives. How many kinds do you really know?
A wide range of plastic additives , is a large class of additives for plastic molding products. Commonly used plastic additives include the following categories:
Flame retardant
Most of the plastic products are flammable, which brings many hidden dangers to the safety of the application of the products. Accurately speaking, flame retardants are more suitable as flame retardants, because "flammable" contains two meanings of flame retardant and smoke suppression, and the concept of flame retardants is more extensive. However, for a long time, people have become accustomed to the concept of using flame retardants, so the flame retardant referred to in the literature is actually a general term for flame retardant and smoke suppressing functional additives.
Flame retardants can be classified into additive flame retardants and reactive flame retardants depending on the mode of use. Additive flame retardants are usually added to the base resin in an additive manner, and they are simply a simple physical mixture with the resin; the reactive flame retardant is generally a monomer containing a flame retardant element and a reactive group in the molecule. Such as halogenated anhydride, halogenated bisphenol and phosphorus-containing polyol, etc., due to reactivity, can be chemically bonded to the molecular chain of the resin, becoming part of the plastic resin, most reactive flame retardant structures are synthetically added flame retardant Monomer of the agent. According to the chemical composition, the flame retardant can be further divided into an inorganic flame retardant and an organic flame retardant. Inorganic flame retardants include aluminum hydroxide, magnesium hydroxide, barium oxide, zinc borate and red phosphorus. Organic flame retardants are mostly halogenated hydrocarbons, organic bromides, organic chlorides, phosphates, halogenated phosphates, nitrogen. It is a flame retardant and a nitrogen-phosphorus intumescent flame retardant. The role of the smoke suppressant is to reduce the amount of smoke and the release of toxic and harmful gases, mostly molybdenum compounds, tin compounds and iron compounds. Although cerium oxide and zinc borate also have smoke suppressing properties, they are often used as flame retardant synergists and are therefore classified as flame retardant systems.
Plasticizer
Plasticizers are a class of additives that increase the plasticity of polymer resins, impart softness to the product, and are the largest class of plastic additives to date. Plasticizers are mainly used in pvc soft products, and are also widely used in polar plastics such as cellulose.
The types of compounds involved in plasticizers generally include phthalates, fatty dicarboxylates, trimellitates, polyesters, epoxy esters, phenyl sulfonates, phosphates, and chlorinated paraffins. Especially phthalates are the most important.
Heat stabilizers
Unless otherwise stated, heat stabilizers refer specifically to stabilizers used in the processing of polyvinyl chloride and vinyl chloride copolymers. Polyvinyl chloride and vinyl chloride copolymers are heat-sensitive resins, which are very easy to release hydrogen chloride during heat processing, thereby causing heat aging degradation reaction. Heat stabilizers generally achieve the purpose of heat stabilization by absorbing hydrogen chloride, replacing active chlorine and double bond addition.
The types of heat stabilizers widely used in industry generally include base-based stabilizers such as salt-based lead salts, metal soaps, organotins, and organic oximes, and epoxy compounds, phosphites, polyols, and Organic auxiliary stabilizers such as ketones. The composite stabilizers, which are composed of main stabilizers, auxiliary stabilizers and other auxiliaries, play an important role in the heat stabilizer market.
Light stabilizer
Light stabilizers, also known as UV stabilizers, are a class of stabilizers used to inhibit the photo-oxidative degradation of polymer resins and improve the weatherability of plastic products. Light stabilizers can be classified into light shielding agents, ultraviolet light absorbers, excited state quenchers, and radical scavengers, depending on the stabilizing mechanism. Most of the light shielding agents are carbon black, zinc oxide and some inorganic pigments or fillers, which are achieved by shielding ultraviolet rays. The ultraviolet absorber has a strong absorption effect on ultraviolet rays, and the harmful light energy is converted into harmless heat energy release by intramolecular energy transfer, thereby preventing the polymer resin from absorbing ultraviolet energy and inducing photooxidation reaction. There are many types of compounds involved in the ultraviolet absorber, and mainly include benzophenone compounds, benzotriazole compounds, salicylate compounds, substituted acrylonitrile compounds, and triazine compounds. The excited state quencher is intended to quench the energy on the excited polymer molecule, returning it to the ground state, preventing it from further causing the polymer chain to break. Excited quenchers are mostly nickel complexes. The radical scavenger has a hindered amine as a functional group, and its corresponding nitroxide radical is the basis for capturing polymer radicals, and since the nitroxide radical is regenerative in the stabilization process, the light stabilizing effect is very prominent. So far, it has developed into the category of light stabilizers with the most varieties and the largest production and consumption. Of course, the role of hindered amine light stabilizers is not limited to the capture of free radicals. Studies have shown that hindered amine light stabilizers often have the effect of simultaneously decomposing hydroperoxides and quenching singlet oxygen.
Foaming agent
It is used in a polymer compounding system to obtain a polymer product having a microporous structure by releasing a gas, and an auxiliary agent for the purpose of reducing the apparent density of the product is called a foaming agent. The foaming agent can be classified into two main types of physical foaming agents and chemical foaming agents according to the manner in which the gas is generated during the foaming process.
Physical blowing agents generally rely on changes in their physical state to release gases, mostly volatile liquid substances, chlorofluorocarbons (such as Freon), low alkanes (such as pentane) and compressed gases are representative of physical blowing agents.
The chemical foaming agent is foamed based on the gas released by chemical decomposition, and is classified into an inorganic chemical foaming agent and an organic chemical foaming agent according to the structure. Inorganic foaming agents are mainly heat sensitive carbonates (such as sodium carbonate, ammonium bicarbonate, etc.), nitrites and borohydrides, which are characterized by heat absorption during the foaming process, also known as endothermic hair growth. Foaming agent. Organic foaming agents have a prominent position in the plastic foaming agent market. Representative varieties include azo compounds, N-nitroso compounds and sulfonyl hydrazides. The foaming process of the organic foaming agent is often accompanied by an exothermic reaction, and is also known as an exothermic blowing agent. In addition, some auxiliaries which adjust the decomposition temperature of the blowing agent, that is, the foaming auxiliaries are also among the foaming agents.
Antistatic agent
The function of the antistatic agent is to reduce the surface resistance of the polymer article and eliminate the electrostatic hazard that may result from static buildup. Antistatic agents can be classified into two types, an internal type and a coated type, depending on the mode of use.
The internal antistatic agent is added to the plastic formulation by adding or blending, and migrates from the inside to the surface or forms a conductive network after molding, thereby achieving the purpose of reducing the surface resistance and discharging charge.
The coating type antistatic agent adheres to the surface of the plastic article by coating or wetting, thereby absorbing moisture in the environment to form an electrolyte layer capable of discharging charges.
From the point of view of the composition of chemical substances, traditional antistatic agents are almost exclusively surfactant compounds, including quaternary ammonium salt cationic surfactants, alkyl sulfonate anionic surfactants, alkanolamines, A nonionic surfactant such as an alkanolamide or a polyhydric alcohol fatty acid ester. However, the emerging "high molecular weight permanent antistatic agents" break this convention. They are generally hydrophilic block copolymers that blend with the base resin in a manner that blends the alloy to conduct charge by forming conductive channels. Compared with surfactant antistatic agents, this high molecular weight permanent antistatic agent is not lost by migration, volatilization and extraction, so the antistatic property is stable and stable, and is rarely affected by environmental humidity.
Mold inhibitor
Antifungal agents, also known as microbial inhibitors, are a class of stabilizing auxiliaries that inhibit the growth of microorganisms such as molds and prevent the degradation of polymer resins by microbial attack. Most polymer materials are not sensitive to mold, but they have mold susceptibility due to the addition of plasticizers, lubricants, fatty acid soaps, etc., which can be used to mold molds. Plastic antifungal agents contain many chemical substances. Commonly used varieties include organometallic compounds (such as organic mercury, organotin, organic copper, organic arsenic, etc.), nitrogen-containing organic compounds, sulfur-containing organic compounds, and halogen-containing organic compounds. And phenolic derivatives and the like.
Brightener
A fluorescent brightener is a fluorescent dye, or white dye, and a complex organic compound. Its characteristic is to stimulate the incident light to produce fluorescence, so that the dyed material has the effect of sparkling like fluorite, so that the material seen by the naked eye is very white.
Filler
Filling and reinforcement are important ways to improve the physical and mechanical properties of plastic products and reduce the cost of blending. Reinforcing materials involved in the plastics industry generally include fibrous materials such as glass fibers, carbon fibers, and metal whiskers. Filler is a kind of incremental material with low compounding cost, including calcium carbonate, talcum powder, clay, mica powder, silica, fly ash, red mud, natural minerals such as wood powder and cellulose, synthetic inorganic Materials and industrial by-products.
In fact, it is difficult to distinguish between enhancers and fillers because almost all fillers have a reinforcing effect. Due to the large amount of fillers and reinforcing agents in plastics, some have become an industry system, and it is customary not to discuss in the category of processing aids. It should be noted that the nano-filled reinforcing materials widely studied today have far exceeded the filling and reinforcing significance of plastics, and their application will bring a new revolution to the plastics industry. Coupling agents are surface modifiers for inorganic and natural fillers and reinforcing materials. Due to the reinforcement in the plastics industry and the filler materials are mostly inorganic materials, the amount of compounding is large. When directly combined with organic resins, plastic complexes are often processed and processed. Decline in application performance. As a surface modifier, the coupling agent can organically surface the inorganic material by chemical action or physical action, thereby increasing the amount of compounding and improving the processing and application properties of the complex. The coupling agents reported in the past generally include long carbon chain fatty acids, silane compounds, organic chromium compounds, titanate compounds, aluminate compounds, zirconate compounds, and anhydride grafted polyolefins.
Crosslinker
The cross-linking of plastics is not much different from the vulcanization of rubber, but it is not exactly the same in the use of cross-linking aids. The cross-linking mode of the resin mainly includes radiation crosslinking and chemical crosslinking. The organic peroxide is the most widely used crosslinking agent type in the industry. Sometimes in order to increase the degree of crosslinking and the speed of crosslinking, it is often necessary to use some co-crosslinking agents and cross-linking accelerators. The cross-linking agent is used to inhibit the free radical cleavage reaction of the organic peroxide cross-linking agent in the cross-linking process of the polymer resin main chain, improve the cross-linking effect, and improve the performance of the cross-linked product. Polymer free radicals. Cross-linking accelerators are mainly used to speed up the crosslinking and shorten the crosslinking time. Curing agents for thermosetting plastics such as unsaturated polyesters and epoxy resins are also in the category of crosslinking agents, such as organic amines and organic acid anhydrides. In addition, the photosensitizer used in the ultraviolet radiation crosslinking process can also be regarded as a crosslinking assistant.
Dispersant
We know that plastic products are actually a mixture of base resin and various pigments, fillers and auxiliaries. The degree of dispersion of pigments, fillers and auxiliaries in the resin is crucial to the performance of plastic products.
Dispersant is an auxiliary agent that promotes uniform dispersion of various auxiliary materials in the resin, and is mostly used for masterbatch, coloring products and high-filled products. Including hydrocarbons (paraffin oil, polyethylene wax, oxidized polyethylene wax, etc.), fatty acid soaps, fatty esters and fatty amides.
Lubricant
Lubricant is a processing modifier that is blended in a polymer resin to reduce the intermolecular friction between resin particles, resin melt and processing equipment, and in the resin melt to improve fluidity and mold release during molding. It is mostly used in the processing of thermoplastics, including hydrocarbons (such as polyethylene wax, paraffin, etc.), fatty acids, fatty alcohols, fatty acid soaps, fatty acid esters and fatty amides.
Release agent
The release agent can be applied to the surface of the mold or the processing machine, or can be added to the base resin, so that the model product can be easily released from the mold and the surface smoothness is improved. The former is called a coating release agent, and is a release agent. The main body, the latter is an internal release agent, and has the characteristics of easy operation and the like. Silicone oils are the most widely used type of release agent in the industry.
Main Control Valve for Komatsu excavator PC50MR-2 PC60-7 PC70-8 PC130-7 PC160-7 PC200-7 PC200-8 PC300-7 PC300-8 PC400-7 PC400-8.
Volvo Excavtor EC210 EC240 EC290 EC330 EC360 EC460 Control Valve, Hyundai R210 R250 R320 Control Valve, and so on.
Packaging Detail:
1. Acquiescently neutral packing
2. According to the customers' request
Delivery Detail: Within 20 days after deposit
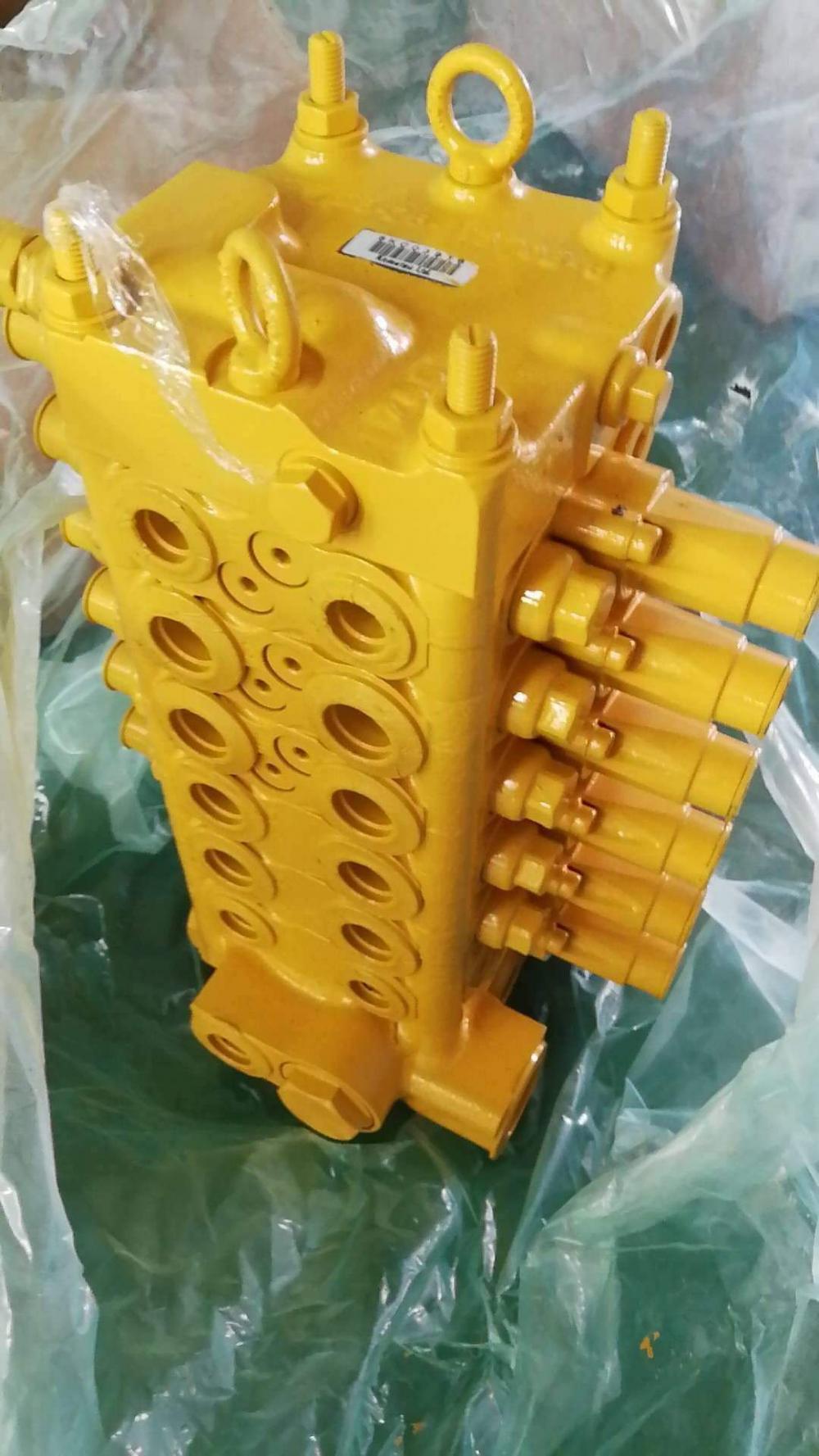
Main Valve,Hydraulic Excavator Main Valve,Main Control Valve,Main Water Valve
Jining Tongderui Construction Machinery Co., Ltd. , https://www.tdr-excavatorparts.com