Talking about the characteristics of various drying equipment - fluidized bed drying equipment
I. Overview of the drying process of fluidized bed drying equipment Fluidized bed drying equipment, also known as fluidized bed drying equipment, the drying characteristics of the drying equipment, the granular solid materials are added to the fluidized bed drying equipment by a rotary feeder, and the air has a blower. It is sent to the combustion chamber, heated and sent to the bottom of the fluidized bed to be distributed and solid material is released to form a fluidized state, and the heat and mass exchange of the gas-solid phase is achieved. After the material is dried, it is sent out from the discharge port. The exhaust gas is discharged from the top of the fluidized bed and recovered by the cyclone collector. The product that is taken out is then evacuated after passing through the scrubber and the mist separator.
Second, the characteristics of fluidized bed drying equipment Fluidized bed drying equipment has the following specific characteristics, the drying equipment is suitable for the drying of non-agglomerating granular materials, the particle diameter can be from 30um-6um; the drying equipment has a simple structure, production The capacity is from tens of kilograms per hour to 400,000 kilograms per hour; the thermal efficiency is about 70%. When removing the combined moisture in the material, the thermal efficiency is about 30%-50%, and the volumetric heat transfer coefficient can reach 2326-6978W/( m?.°C); the residence time of the material in the fluidized bed is related to the structure of the fluidized bed. If the design is reasonable, the residence time of the material in the fluidized bed can be arbitrarily prolonged. The disadvantage is that the resistance of the hot air through the distribution plate and the material layer is relatively large, generally about 490-1470 Pa. The energy consumption of the blower is large. The material of the single-layer fluidized bed drying equipment is completely mixed in the fluidized bed, and some materials may go shortly and directly fly to the outlet from the feeding port to the discharging port, resulting in uneven drying of the materials. In order to improve the uniformity of drying of the materials in the fluidized bed, fluidized beds of different structures are generally used. Such as a single-layer fluidized bed with a baffle structure for controlling material short-circuit, a horizontal multi-chamber fluidized bed, a multi-layer fluidized bed, and the like.
The multi-layer fluidized bed drying device can increase the drying time of the material and improve the uniformity of the water content of the dried product, thereby facilitating the control of the dry quality of the product. However, as the number of layers increases in the multi-layer fluidized bed drying apparatus, the distribution plate increases correspondingly, and the bed resistance increases. At the same time, between the layers, the material should be quantitatively transferred from the upper layer to the lower layer, and to ensure a stable vulcanization state, an overflow device must be used. This in turn increases the complexity of the device structure. For the removal of moisture-bound materials, it is appropriate to use a multi-layer fluidized bed. For example, some large-scale pharmaceutical plants use a two-layer fluidized bed drying facility to dry the materials, and dry the aminopenin with a moisture content of 15%-30%. Some polyester textile mills use a five-layer fluidized bed drying equipment. The material is dried and the polyester resin is dried to make the moisture content of the product reach about 0.03%.
The horizontal multi-chamber fluidized bed drying equipment can adjust the air volume of each chamber by dividing into multiple chambers. At the same time, the baffle is added in the fluidized bed to avoid short-circuiting of the materials, and the moisture content of the dried product is relatively uniform. If the air volume and temperature of each room are adjusted in operation, or the hot air of the last few chambers is used once, or an internal heater is added, the thermal efficiency can be improved.
Through this introduction, we have a new understanding and understanding of fluidized bed drying equipment, which can increase the unnecessary waste of resources and low product quality in the use of fluidized bed drying equipment.
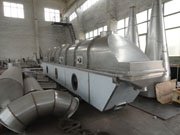
1. Product introduction
Coal-based Column Denitrification Column Activated Carbon is cylindrical black particles. It has many characters, such as high porosity, high sulfur capacity, high desulfurization efficiency, large surface area, light weight, strong adsorption capacity, wear resistance, good water resistance, low air resistance, easy regeneration, not easy to break under high pressure etc. It is a commonly used in adsorbent.
2. Adsorption purification principle and process
Coal-based denitrification Activated Carbon is divided into large pores (pore size greater than 50nrrt), the middle hole (pore size between 2 ~ 50nm) and micro-pore (pore size less than 2nm) three categories.
The denitrification activated carbon is by active carbon`s adsorption and catalytic activity of activated carbon. The strong catalytic effect of the active carbon for sulfur dioxide in gas, and a small amount of Oxygen in the oxidation reaction, the reaction of elemental S adsorbed the surface of activated carbon. When activated carbon desulfurization agent the adsorption reaches saturation, the desulfurization efficiency decreased obviously, it must carry on the regeneration. The regeneration of active carbon adsorption depends on the material, sulphur began to melt under atmospheric pressure is 190 degrees, 440 degrees Celsius will sublimate into gas, therefore, the general use of superheated steam temperature of about 450-500 degrees Celsius for the regeneration of activated carbon desulfurization agent. When the desulfurization agent reach high temperature, the elemental sulfur separate out activated carbon, the precipitation of sulfur into sulfur recovery pool, water cooled to form solid sulfur.
Column Denitrification Column Activated Carbon
Activated Carbon,Column Denitrification Column Activated Carbon,Air Purification Activated Carbon
Ningxia XingKai Silicon Industry Co., Ltd. , http://www.xingkaisic.com