Research on Forging Technology of Bearing Rings
2023-08-08 14:10:28
The forging process is a piece of material that is cut into two ferrules after being cut by the sleeve, and only one leather core is produced, which will improve the material utilization rate and reduce the manufacturing cost. In addition, it can be the same type of inner and outer ring forging, which is conducive to the production organization and management, or can be forged by two sets of different types of ferrules, flexible and changeable, and suitable for mass production.
1. Program development
The process route is shown in Figure 1. The process plan has the following technical features:
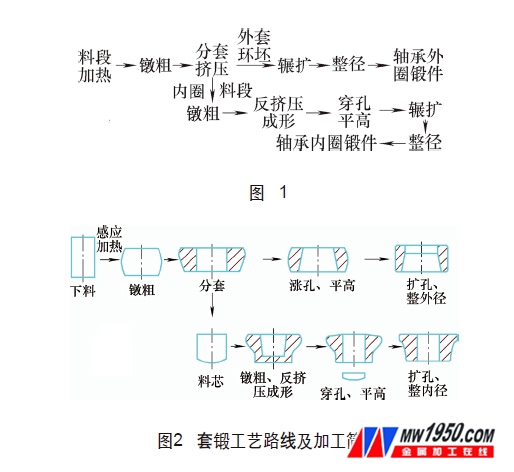
(1) The medium frequency induction electric furnace is used to replace the heating material of the original gas heating furnace, the heating speed is fast, the oxidation loss is small (the burning loss rate is about 0.5%, which is 1/4 of the gas furnace), and the heating quality is good (the temperature uniformity of the material section is good) ), the thermal efficiency is high, the labor intensity of workers is greatly reduced, and it is easy to realize automation, which provides conditions for effective control of heating. In addition, the soot, dust and high temperature stubbornness that have long plagued the working environment will be fundamentally treated. The CO 2 waste gas will no longer be discharged, and the noise pollution of the blower will not exist anymore. It will achieve a double harvest of economic and social benefits.
(2) The forging process is that a material section is expanded into two ferrules after being cut by the sleeve, and only one leather core is produced, which will improve the material utilization rate and reduce the manufacturing cost. In addition, it can be the same type of inner and outer ring forging, which is conducive to the production organization and management, or can be forged by two sets of different types of ferrules, flexible and changeable, and suitable for mass production.
(3) The two ferrules produced by the process plan adopt the full diameter, eliminating the ellipse and taper, and achieving the purpose of uniform size and improved geometric precision. It offers the possibility to further compress the allowance and tolerance.
2. Analysis of specific implementation process and technical difficulties
Take the forging process of the inner ring of a tapered roller bearing as an example.
(1) Determine the reasonable process and processing method according to the process route, and determine the process and processing method of the inner and outer ring sleeve forging of the tapered roller bearing, as shown in Figure 2.
(2) Design the inner ring forgings according to the process plan and determine the weight of the blank. According to the processing capability, performance and accuracy of the medium frequency electric induction furnace, press, reaming machine and warping machine on the set of forging production line, the retention and tolerance of the inner outer ring forgings are determined, and the inner ring ring raceway is formed. The expanded plan draws a forging diagram, as shown in Figure 3.
Cutting weight calculation method
Appeared in the following formulas
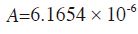
Outer ring forging weight
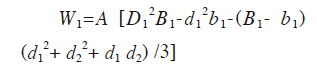
Inner ring forging weight
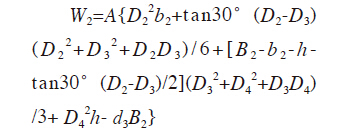
According to the inner diameter dimension d3 and the height dimension B2 of the inner sleeve forging , a certain expansion ratio is selected to determine the diameter D5 of the punch when the inner sleeve is reversely squeezed. Even leather core weight W 3 = 8D 5 2 A
The medium-frequency induction heating oxidation ignition coefficient is selected to be 0.5%~1.0%.
Calculate the weight of the blank

According to the principle of length-to-diameter ratio of material forging 1.5, select the appropriate bar diameter, finally determine the bar diameter and the length of the material, and then select the appropriate cutting equipment according to the weight of the blank and the diameter of the bar (select S-QA42-500B type precision Bar shearing machine).
(3) The principle of medium-frequency induction heating in the heating process of the material section is to use the metal “super-skin†effect to generate an alternating magnetic field in the inductor, and an alternating eddy current is generated inside the metal blank. The metal billet is directly heated by eddy current heating and magnetization heating, thereby avoiding the problem of uneven heating temperature of the metal billet. The heating speed is fast, the oxidation loss is small, the heating quality is good and very stable, and it is easy to realize automation, which creates conditions for effective control of heating temperature.
The key point of the transformation of the intermediate frequency induction heating furnace is to increase the infrared heating temperature control device to control the forging temperature of the blank and solve the problem of uneven heating temperature of the heavy oil heating furnace. The control principle is as follows: a temperature sensing probe is arranged at the discharge port, the temperature signal is received, the temperature signal is converted into an electrical signal by the sensor, and the forging temperature is dynamically reflected on the temperature digital display, thereby achieving continuous control of the heating temperature. .
(4) The sub-assembly process is the key process for the whole set of forging success. The function is to separate the inner cover blank from the outer cover blank, and it is necessary to ensure that the inner and inner rings are evenly distributed with the weight of the leather core, and The dimensions of the outer ring blank and the large core are separated to meet the requirements for further processing, as shown in FIG.
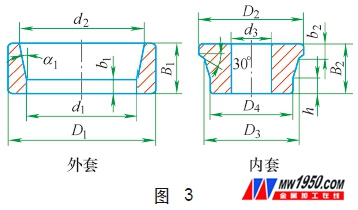
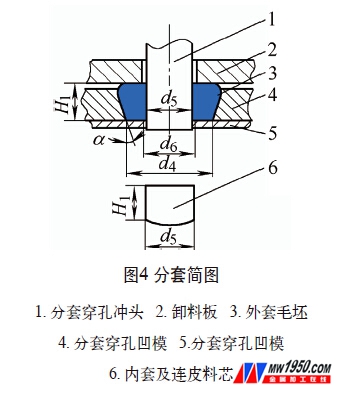
Figure 3: Selection of various sizes: 1 According to the height B1 of the outer casing forging, the height of the outer ring of the outer casing is determined to be H1=B1+(5-10) mm. 2 Because Ad52 H1=W2+ W3, the diameter of the split punch d5 can be determined. 3 According to the law of volume invariance, the cross-sectional area of ​​the lower end of the outer ring of the outer casing should be equal to the cross-sectional area of ​​the small end of the forging. Therefore, the sub-sleeve supports the inner diameter dimension d4= of the lower end of the die. The 4-piece support concave mold inner surface angle α 2 should be approximately equal to the outer ring inner cone angle α 1 . 5 In the production process, the lower end face of the outer ring of the outer casing and the upper end face of the inner casing blank have been burred, which will cause the end face to fold during the subsequent expansion process, which may cause the product to be scrapped.
After repeated observations and tests, the following three factors were found to affect the generation of burrs: when the temperature was high, the burrs appeared. Therefore, we strictly controlled the temperature at 1050 °C and kept stable. The head and the sub-sleeve perforated die gap. After repeated trials, it is finally determined that d6-d5=(2~2.5)mm; the gap between the machine guide rail and the slider. When the gap is large, the punch and the die will be injured due to the eccentric load, resulting in a burr burr, so a small amount of clearance between the machine guide rail and the slider should be maintained.
(5) The outer ring blank formed after the splitting process is a straight blank in the outer cone, which is too different from the shape of the outer ring forging, and cannot be directly expanded on the reaming machine. So we designed a dilating punch that swells the inner diameter into a conical shape, and the outer diameter expands to a nearly straight shape, which is close to the shape of the outer ring to facilitate the expansion (see Figure 5).
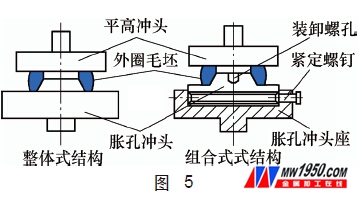
The left figure in Figure 5 shows the initial expansion process, and the right picture shows the improved expansion process. The main difference between the two figures is the structural design of the punch under the expansion hole. From the left picture we can see that the expansion punch is a whole, and the effective working surface accounts for less than 1/5 of the whole volume. That is to say, the worker has to do 4/5 useless work in changing the model or adjusting the blank size. We probably calculated that the punching punch is the lightest and has 20kg, which increases the workload of disassembly and installation, which is very inconvenient for the adjustment work. In addition, the punch is specially designed for a specific type 7 bearing jacket, so it cannot be effectively reused, which causes a large waste of the mold and increases the production cost. The dilating punch is then designed as a combination. As seen in the image to the right, the undercut punch and the undercut punch seat. This improvement makes the effective working area of ​​the punching punch more than 50%, the weight is reduced from the original 20kg to 9kg, and the disassembly is convenient. It is easy to loosen the set screw and screw it into the loading and unloading screw hole. Remove the punching punch. In this way, the mold adjustment becomes convenient, and the labor intensity is greatly reduced, and the mold cost is saved.
(6) Inner sleeve blank forming process Tapered roller bearing inner ring forming è¾— expansion and forging has always been one of the technical difficulties in the industry. In particular, the blank forming method not only ensures the rational distribution of the axial material of the ferrule, but also considers the force of the equipment during forming, and skillfully allows the metal to flow in the direction of minimum resistance. The fully enclosed positive extrusion forming process of the original small conical inner sleeve forgings cannot be adopted because the equipment is unreasonably stressed, and the back extrusion process cannot meet the material distribution requirements. So we invented a new semi-closed reverse extrusion forming process by inspection and experiment, as shown in Figure 6.
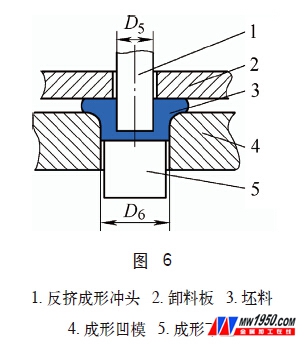
It can be known from the law of volume invariance before and after forging that the cross-sectional area of ​​the small end face of the blank should be equal to the cross-sectional area of ​​the small end face of the inner set forging, so the inner diameter of the forming die, that is, the outer diameter of the small end face of the blank can be calculated. Since the weight of the inner ring and the weight of the continuous leather core are fixed after the sub-sleeve, as shown in Fig. 6, the metal material below the large rib of the inner ring is formed inside the forming die at the time of extrusion molding, and the weight is guaranteed by the size of D5 and D6. The metal material of the rib part is controlled by the unloading plate, the outer diameter is open, and the weight is controlled by the blank when the sleeve is set. This is the characteristic of the semi-closed reverse extrusion forming process, which not only ensures the shape of the blank after extrusion, but also can reasonably The material is distributed along the axial direction while ensuring the rationality of the force of the equipment. After the forming is completed, the billet is flattened and then expanded on the reaming machine.
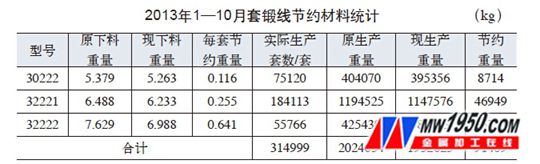
(7) The conical inner casing ring on the reaming machine is formed on the D51-250 reaming machine. It is a mature process in the forging factory. The key is to master the dimensions and geometric tolerances of the finished forgings, and give the next step. A reasonable diameter is reserved for the whole diameter.
(8) Whole diameter process In order to improve the machining efficiency of the lathe and reduce the processing difficulty, it is decided to carry out the outer diameter of the outer casing; the inner diameter of the inner casing is set, and the inner casing ring is kept to have a full diameter of 0.5 to 1.5 mm. It avoids defects such as the size geometric tolerance and the large diameter of the large diameter due to the small diameter.
3. Analysis of economic and social benefits
As can be seen from the attached table, from January 2013 to October 2013, the number of 30222 and other three models, about 315,000 sets, was actually saved compared with the original process (GCr15) 91.4 t. It can be seen that the forging process not only saves materials, reduces costs, improves the competitiveness of enterprises, but also achieves remarkable results in environmental protection.
4. Conclusion
The set of forging is the simultaneous production of two ferrules by one heating. The use of this method to produce tapered roller bearings can effectively save materials and increase production, thereby improving the competitiveness of enterprises. The use of a medium frequency induction furnace instead of a gas furnace to heat the bar material not only reduces the oxidation of the bar, but also eliminates the emission of carbon dioxide and the noise of the blower, and has achieved remarkable results in environmental protection. Therefore, the overturning process should be widely applied to the bearing ring forging process.
About the author: Luo Qiang, Wang Yujie, Wang Zhanye, Luoyang LYC Bearing Co., Ltd.
Lock cylinder,Door lock cylinders,Mortise lock cylinder
Wenzhou Shenghong Metal Products Co.,Ltd , https://www.shenghonglock.com