Application of TD processing in special vehicle cold working die
2023-08-10 14:12:07
At present, the design of high-strength steel body structure has become a development trend. By optimizing the body structure, it can not only improve the performance of the vehicle, but also significantly reduce the body quality. After several years of development, high-strength steel has been widely used in the compartments of heavy mining vehicles and road dump trucks, girders, beams and fences of semi-trailers.
As a high-strength steel, one of the best methods for lightweighting, its high strength brings challenges to the use of cold-working dies, especially in the use of forming dies, which tend to cause strain on the surface of the mold during use and also make the surface of the workpiece Pulling occurs, and the squeezing of the bristles not only affects the quality and appearance of the coating, but also tends to cause stress concentration, which affects the life of the vehicle. For example, the semi-trailer corrugated plate mold often causes the surface of the mold to be pulled in the process of pressing the high-strength steel plate, causing the work to stop. After the grinding of the mold is used to polish the surface of the mold, the work can be carried out to bring the production organization to the production organization. A lot of inconvenience.
1. Principles of TD processing technology
In the 1970s, the Toyota Central Research Institute of Japan developed the TD treatment technology, namely the metal carbide diffusion coating, which is called molten salt metal in China. The technology is to place the workpiece in a borax molten salt and its special medium at a certain processing temperature (generally 850~1050 °C), and generate a chemical reaction through the metal atom in the special molten salt and the carbon and nitrogen atoms in the workpiece. Diffusion on the surface of the workpiece to form a layer of metal carbide such as vanadium, niobium, chromium, titanium, etc. from a few microns to more than 20 microns. The coating has extremely high hardness and hardness of up to about 3200 HV. It has extremely high wear resistance, seizure resistance, corrosion resistance, etc. The coating is dense and smooth, combined with the metallurgy of the substrate, and can be repeatedly treated repeatedly. The most effective and economical solution to the above-mentioned cold forming mold strain problem can increase the life of the workpiece several times to several tens of times, and has extremely high application value.
2. TD processing process
The TD treatment cycle is generally about 3 days. The process flow is: pre-treatment (polishing, preheating, stirring) → tempering → cleaning → inspection → TD treatment (molten salt impregnation) → quenching → adjustment tolerance → post-treatment. The purpose of preheating is to prevent deformation, dimensional change and crack generation of the mold. The preheating temperature of the small mold is 520 ° C, and the preheating temperature of the larger mold can be appropriately increased. Preheating should be sufficient, but make sure that no oxide layer is formed on the surface. The TD treatment temperature is 900~1030 °C, and the TD layer can be formed in this temperature range. The immersion time is selected according to the mold material. In principle, the small mold is 7~8h, and the large mold is 12~14h, which can be adjusted according to the situation. After completion of the molten salt immersion, the mold is subjected to salt bath quenching and cooled in a salt bath at 500 ° C, and it is necessary to pay attention to the speed from the molten salt bath to the quenching salt bath to prevent oxidation of the TD permeable layer during movement. After cooling for a period of time, the mold parts are lifted out, slowly cooled to 60~70 °C, and the quenching process is completed. The surface temperature of the mold is measured and it must be tempered immediately at 60~70 °C.
3. Mechanical properties after TD treatment
After TD treatment, the mechanical properties of high strength steel will change.
(1) Wear resistance is stronger than hard alloy.
(2) Peel resistance is stronger than vapor deposition coating (PVD, CVD, PCVD) and hard chromium plating.
(3) The hardness is stronger than that of hard alloy, and the hardness is as high as 2500~3600HV. When it is lowered from high temperature to normal temperature, it can return to the original normal temperature performance.
(4) Corrosion resistance is stronger than stainless steel.
(5) Strong oxidation resistance.
4. TD processing should pay attention to matters
(1) The material of the mold for TD treatment needs to be chrome steel material with wC>0.3%. After several years of exploration and application, the following materials are recommended for cold work die steel: domestic grades: Cr12Mo1V1, Cr12MoV, Cr5Mo1V. Japanese brands: SKD11, SLD, DC53.
US grades: D2, A2, D3. The cold work die steel grades suitable for TD treatment are shown in the attached table.
(2) Surface roughness of mold working surface before TD treatment: Ra≤0.8μm.
(3) Heat treatment requirements: quenching must be carried out before TD treatment.
(4) Before the TD treatment, it is necessary to confirm the dimensions, matrix hardness, material and appearance defects, and check for cracks.
(5) Due to the limitation of TD processing equipment and cost, most domestic TD processing enterprises can only process molds within 500mm×1000mm. Exceeding this size, it is necessary to adopt a sub-block structure.
5. Application of TD processing technology
Due to its excellent strengthening effect, TD processing technology is widely used to solve the problem of strain and wear between the mold and the workpiece or between the workpiece and the workpiece caused by various types of wear. Among them, TD treatment is one of the best solutions in the world due to strain or pulling caused by occlusion or sticking. If there is no TD processing technology, the problem of strain on the mold and the workpiece is difficult to solve. Figure 1 shows a typical workpiece processed by our TD-processed mold.
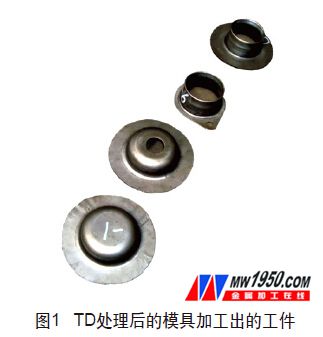
Due to the high cost of TD, it is generally used in processing molds for high value-added parts such as cars and commercial vehicles. As high-strength steel is widely used in special vehicles, in order to improve product quality and improve mold life, TD processing technology is gradually accepted by special-purpose vehicle manufacturers, and is deep drawing, bending, flanging, cold rolling, punching, and cold. The application is obtained by extrusion and Other molds, and the mold block after TD treatment is shown in FIG. 2 .
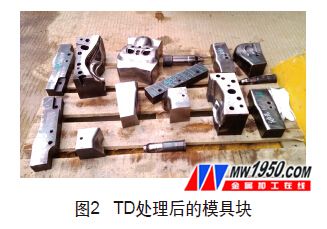
6. TD cladding mold maintenance and maintenance
The molds processed by TD coating need to be carefully maintained and carefully maintained. After each batch of parts is stamped, the mold should be cleaned, especially the deep drawing forming mold. The mold punch, the die and the pressure ring should be disassembled, rinsed with hot water, and the foreign matter such as oil stains and iron filings should be removed. The compressed air is blown dry to avoid rust. The cleaned mold can not only ensure the quality of the stamping parts in the next use, but also the most important thing is to ensure that the TD coating is not damaged and the service life of the mold is improved.
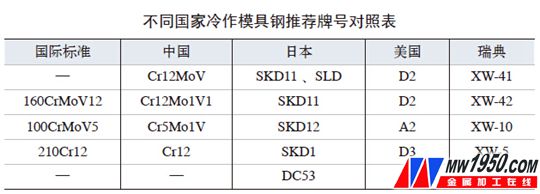
7. Conclusion
At present, TD processing technology has been applied to many cold forming molds such as forming and punching in our company. It has been proved by practice that TD processing will greatly improve the wear resistance of the mold surface and the toughness of the base metal. Under normal conditions and ordinary molds. In comparison, its service life is increased by more than 8 times, and the defective rate of the product is reduced by more than 10%, which also saves the number of repeated mold repairs and molds.
About the author: Ge Zhiqiang, Han Yueqin, Chen Yunhai, Lu Jingping, Zhumadian CIMC Huajun Vehicle Co., Ltd., Technology Center.
Refrigeration Parts,Leader Refrigeration Parts,Refrigeration Parts And Supplies,Refrigeration Compressor Parts
Ningbo Kyson Cool Electronic Technology Co., Ltd. , https://www.kysoncool.com